(GGBFS)Ground Granulated Blast furnace Slag
Product name : (GGBFS)Ground Granulated Blast furnace Slag
Products Category: > (GGBFS)Groud Granulated Blast Furnace Slag
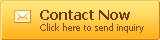
Product name : (GGBFS)Ground Granulated Blast Furnace Slag
Details :Ground Granulated Blast Furnace Slag (GGBFS) is a recyclable material created when the molten slag from melted iron ore is quenched rapidly and then ground into a powder.
Generally, GGBFS concretes develop strength more slowly than Ordinary Portland Cement (OPC) concretes, but will exhibit higher strength after one year. GGBFS concretes are also less permeable, but they can develop abnormal air void systems. The performance of GGBFS concretes depends not only on the amount of GGBFS used, but also on the chemical composition of the other materials in the mixture. Three different GGBFS replacement levels will be studied in this part of the project: 0%, 30%, and 50%. Thirty percent is the most commonly used replacement level. This means that of the cemetitious material in the concrete, 30% is GGBFS, and 70% is OPC. The project will investigate the performance versus a 100% OPC concrete (0% GGBFS), and will also determine whether a 50% level is a reasonable replacement level. Along with the GGBFS replacement level variable, four different cement brands and two coarse aggregate types will be used to determine its performance with different materials. There will also be mixtures created and cured in 40o F conditions to determine the performance of GGBFS concrete at lower temperatures.
GGBFS concretes have proved to be susceptible to surface scaling. The reason for this poor performance characteristic is not yet known and will be investigated in this project. Previous studies have shown that carbonation in the concrete's top layer could be a major cause of the decreased scaling resistance in GGBFS concrete. Twelve mixtures will be tested for scaling resistance. Again, 0%, 30% and 50% GGBFS replacement levels and two coarse aggregates will be tested. Two cement brands will be studied. For each mix, there will be four different curing conditions for the sample blocks. In addition, two curing methods to reduce carbonation in the concrete will be investigated at the 30% and 50% replacement levels. The blocks will be ponded with a salt water solution and subjected to cyclic freeze-thaw conditions for 60 to 100 days. After every five cycles, the amount of scaling will be measured.